We detected, that your browser supports another language than the called one. This page is also available in your language! Would you switch to this page in your language?

STABLE CONSTRUCTION
Maximum stability, both statically and dynamically, is ensured by the compact monoblock structure made from polymer concrete. Ultimate process accuracy guaranteed.
MODERN DESIGN
The design is compact and ergonomic, with every detail carefully considered. Perfect for everyday work, maintenance and servicing.
OPTIMAL ACCESSIBILITY
The control cabinet and the maintenance compartment doors are perfectly accessible and the deep-set operation doors open wide. The machine can even be loaded through an open roof with a crane.
IOT GATEWAY AS STANDARD
The keyword is Industry 4.0: Our machines are communication-enabled. An IoT gateway is fitted as standard and this opens the door to the digital world for you.
COOLANT TANK
Thanks to the coolant return flow, no coolant tank – in which dirt and grinding residue could settle – is required. No dirt means no cleaning. Fewer maintenance tasks. More time for what matters most.
MOST ADVANCED DRIVE TECHNOLOGY
Both machines are equipped with powerful servo technology. Saving energy and space, and easy to service. Designed for complex sequences for shorter machining times and maximum productivity.
ULTRA-SIMPLE OPERATION
The machines are operated via the touch screen or keypad, along with the established workshop-oriented user interface in the familiar design. This offers an override function, which can be used to easily adapt the machining speed.
MANUAL OPERATING UNIT
The manual operating unit offers additional flexibility: Any desired axis can be viewed and adjusted directly on the enclosure – regardless of the control panel.
EXCELLENT STABILITY. MAXIMUM GRINDING PERFORMANCE. OUTSTANDING GRINDING RESULTS.
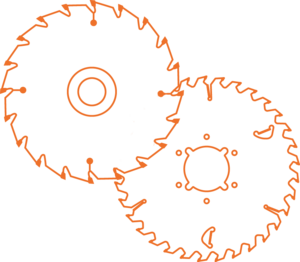
FULLY CN-CONTROLLED
The CS 860 and CSF 860 are two fully CN-controlled machines with 8-axis or 7-axis kinematics.
DIAMETER
Both machines are designed for circular saw blades with a diameter of 80 to 860 mm.
FULLY AUTOMATED SEQUENCES
Both machines feature measuring equipment for fully automated set-up and work processes and numerous additional units for specific applications.
AUTOMATIC LOADING
For maximum efficiency, up to three machines can be loaded automatically in conjunction with the VOLLMER ND handling system.
FOR ALL TOOTH GEOMETRIES
All conceivable surfaces and machining combinations are possible. In a single cycle. It doesn't get more flexible than this.
MADE FOR YOU. AND FOR YOUR APPLICATIONS
- FOR TOOL MANUFACTURERS
For everyone producing, fitting and supplying carbide-tipped circular saw blades. - FOR SHARPENING SERVICES
For service companies that process orders quickly and flexibly. - FOR SAW MILLS
For saw mills with a high daily sharpening workload. - FOR END USERS AND SERVICE PROVIDERS
For service providers offering sawing services or manufacturers of furniture, floors, panels or insulating materials.
SAME CONSTRUCTION. SAME KINEMATICS. CRUCIAL DIFFERENCES.
The CS 860 and CSF 860 look the same and are almost identical in structure, but are characterised by crucial differences. Both machines are based on the same kinematic concept.
STABLE CONSTRUCTION
Maximum stability, both statically and dynamically, is ensured by the compact monoblock structure made from polymer concrete. Ultimate process accuracy guaranteed.
MODERNES DESIGN
The design is compact and ergonomic, with every detail carefully considered. Perfect for everyday work, maintenance and servicing.
OPTIMAL ACCESSIBILITY
The control cabinet and the maintenance compartment doors are perfectly accessible and the deep-set operation doors open wide. The machine can even be loaded through an open roof with a crane.
IOT GATEWAY AS STANDARD
The keyword is Industry 4.0: Our machines are communication-enabled. An IoT gateway is fitted as standard and this opens the door to the digital world for you.
NO COOLANT TANK
Thanks to the coolant return flow, no coolant tank – in which dirt and grinding residue could settle – is required. No dirt means no cleaning. Fewer maintenance tasks. More time for what matters most.
MOST ADVANCED DRIVE TECHNOLOGY
Both machines are equipped with powerful servo technology. Saving energy and space, and easy to service. Designed for complex sequences for shorter machining times and maximum productivity.
ULTRA-SIMPLE OPERATION
The machines are operated via the touch screen or keypad, along with the established workshop-oriented user interface in the familiar design. This offers an override function, which can be used to easily adapt the machining speed.
MANUAL OPERATING UNIT
The manual operating unit offers additional flexibility: Any desired axis can be viewed and adjusted directly on the enclosure – regardless of the control panel.
SOFTWARE
The CS 860 and CSF 860 make it easy for you. Numerous programs and geometries are already stored. Depending on the requirements, the oscillation program, automatic grinding path optimisation, specific measurement programs and advanced multi-surface machining are available as an option.
PRECISE OSCILLATION PROGRAM
The oscillation program offers greater flexibility, optimises the machining process, increases productivity and ensures grinding results of outstanding quality.
ADJUSTABLE CUTTING SPEED
For greater flexibility and optimised processes, the grinding wheel cutting speed can be adapted, in addition to the adjustable feed rate.
AUTOMATIC DETECTION OF REPAIR TEETH
The sensors detect newly inserted teeth and sharpen them to size using oscillating machining. This allows saw blades with newly inserted teeth to be machined in a single set-up.
AUTOMATIC DETECTION OF BROKEN TEETH
In addition to newly inserted teeth, the feed pawl also detects broken teeth, thereby automatically preventing damage to the grinding wheel.
AUTOMATIC DETECTION OF TOOTH PITCH
The feed pawl detects the tooth pitch automatically. No manual entry or setting is required, eliminating the risk of operating errors. Group toothing can also be set up and machined with ease.
AUTOMATIC GRINDING PATH OPTIMISATION
The time-optimised machining software simplifies things greatly for the operator. The grinding start and end are optimised automatically. This results in significant time savings and high process reliability. Benefits that truly pay off.
SMART MEASUREMENT PROGRAMS
Depending on the machining operation, specific measurement programs measure with one tooth, several teeth or all the teeth. And give digital results. This guarantees full quality control.
ADVANCED MULTI-SURFACE PROGRAM
Thanks to the advanced multi-surface program, up to 90 surfaces can be machined. This can be applied to one tooth or split between up to 30 teeth. This means maximum flexibility for you.
HARDWARE
Both machines offer three measuring systems, user-friendly compensation and an adjustable opening distance on the blade clamping mechanism to increase the flexibility of your processes and improve accuracy – all very simply and automatically.
MEASURING CUBE, MEASURING SENSOR AND DEVICE FOR MEASURING STRUCTURE-BORNE SOUND
VOLLMER never comprises on precision. That is why the machines feature three measuring systems: The measuring cube for the tool compensation measurement, which offers absolute process reliability, the measuring sensor, which delivers excellent 3D measurement accuracy, and the acoustic sensor which optimises the set-up procedures. Nothing could be more precise.
COMPENSATION
Instead of a general, overarching compensation, the compensation here is user-friendly and can be assigned either to the circular saw blades or to the grinding wheels. The advantages of this are optimised processes, performance and results.
ADJUSTABLE OPENING DISTANCE ON THE BLADE CLAMPING MECHANISM
The blade clamping mechanism is depressurised during the tooth feed. A wide opening may be required for certain types of saw blade body. Adjusting the opening distance can help increase productivity.
CONTROLLED LATERAL ADJUSTMENT
This enables automatic machining of saws with a clamp in mixed operation. The controlled lateral adjustment turns an 8-axis or 7-axis machine into a 9-axis or 8-axis machine. This additional axis increases flexibility and guarantees high-precision grinding in a single pass. Perfect for machining saw blades in the saw mill industry.
CENTRE BRAKE
Together with the feed pawl, the centre brake makes it possible to use an opening blade clamping mechanism to machine coated saws or saws with scraper blades. This guarantees perfect positioning.
OPERATION
First and foremost, the CS 860 and CSF 860 are simple to operate. All the program data required can be found in two clearly structured programming windows. Clear symbols and a modern design ensure clear orientation. The user interface is tried and tested. The touch screen or keypad are used for operation. And for special applications and servicing – for example, for calibration or referencing – the practical manual control is available as an option. Quite simply, it doesn't get easier or more flexible than this. Load, select a program, done.

MODERN DESIGN
Clear symbols, simple operation and a modern aesthetic. Our display is intuitive for any user to navigate.
TOUCH SCREEN AND KEYPAD
Some love keypads, others prefer touch screens. Many use both. So, the CS 860 and CSF 860 have both. This is not only simple, it is highly practical.
OVERRIDE FUNCTION
The override function acts as a potentiometer, to make speed adjustments in automatic mode as necessary.
TRIED-AND-TESTED USER INTERFACE
Anyone who has already worked with a VOLLMER sharpening machine will already be familiar with this workshop-orientated user interface. Just two programming windows are used for operation.
GRINDING WHEEL MANAGEMENT
The machines have an identical grinding wheel management system. In other words, once grinding wheels have been measured, they do not have to be measured again after replacement. This makes handling easier for the operators.
METRIC AND IMPERIAL SYSTEM
Different countries, different units of measurement. Anyone who uses the imperial system rather than metric measurements can find everything in inches here.
MANUAL OPERATING UNIT
The manual operating unit allows the machine to be operated in any place imaginable – perfect for manual applications, special applications and maintenance tasks without the control panel, to calibrate the axes and machine.
UNIVERSAL FOR TOOTH FACE AND TOOTH TOP.
Greater flexibility: For your sequences too. This is exactly what the CS 860 offers you. A sharpening machine for tooth faces and tooth tops on circular saw blades up to 860 mm. You can enjoy greater flexibility in your programs. You can even combine different sequences across multiple machines.
- HOLLOW FACE GRINDING
The independent grinding unit with a separate grinding motor enables concave tooth faces to be sharpened at very high speeds, ensuring extremely sharp cutting edges. - CHIP BREAKER GROOVE MACHINING
This process enables chip breaker grooves to be machined on saw blades, even with the smallest tooth pitch. In addition, it is also possible to machine the V-shaped groove on the tooth top. - AUTOMATIC ANGLE MEASUREMENT
Measuring the clearance angle, bevel grinding angle and tooth surface increases user convenience, for example when machining a V-shaped groove, and significantly helps to reduce the risk of errors. An external premeasurement is not necessary.
- PRECISE OSCILLATION GRINDING
The oscillation program ensures high removal rates for optimised cutting edges and surfaces, maximum flexibility and supreme process reliability - TRANSVERSE FEED PAWL
Thanks to the transverse feed pawl, the CS 860 and the associated saw blade mount, even chipper segments can be machined easily in manual mode. - AUTOMATIC GRINDING OF TIP GROOVES
For users requiring a CNC machine for grinding tip grooves (production or repair). - AUTOMATIC RELIEF GRINDING PROGRAM
The process releases the body behind the carbide cutting edge. The body is ground back in a separate process. The advantage of this is that both the grinding path on the tool cutting edge and the machining times for the next resharpening tasks are extremely short.
MAXIMUM FLEXIBILITY FOR THE SIDES.
The CSF 860 grinds every side with ease. The 7-axis side grinding machine has CNC and is designed for complete machining of a wide variety of tooth shapes. Reliable, safe, flawless. It enables you and your specialist staff to easily adjust the angle, along with fully automated calibration and work processes.
- MEASURING SYSTEM
The measuring sensor integrated as standard records all the relevant parameters such as the cutting width, blade thickness and tooth surface and uses these to automatically calibrate the machine. - SIMPLE ANGLE ADJUSTMENT
This ensures easy and reliable calibration of different types of saws with different radial and tangential angles. - REPAIR PROGRAM
The repair program increases the flexibility during servicing, and can also be used for multiple surfaces. - MANUAL SYMMETRY CORRECTION
Operators can manually change the symmetry of the cutting edges, for example for blades which are not level.
THE ND HANDLING SYSTEMS. AUTOMATIC AND POWERFUL.
Whether during servicing, with the user or with the manufacturers – VOLLMER has the right ND handling system for everyone who grinds around the clock. How you set it up depends entirely on your capacities and your grinding needs. Discover all the possibilities.

THE ND 230 | 250 | 270 HANDLING SYSTEMS
FOR UP TO 650 SAW BLADES FROM 100 TO 630 MM.
Thanks to the VOLLMER ND handling systems, all options are open to you to make automatic loading variable. Up to three machines can be combined with up to seven loading carriages. Each loading carriage holds up to 50 saw blades, the entire handling system with its 13 loading positions offers you space for up to 650 saw blades which can be machined automatically – around the clock, 24/7
THE ND 320 | 340 | 360 HANDLING SYSTEMS
FOR UP TO 550 SAW BLADES FROM 200 TO 840 MM.
For larger, even heavier circular saw blades up to a diameter of 840 mm, there is the ND 320 | 340 | 360 handling systems: Up to three machines can also be installed in the full configuration, in conjunction with up to six loading carriages including 550 saw blades. Particularly robust double grippers allow saw blades weighing up to 11 kg to be changed quickly. One-sided gripper allocation makes it possible to automatically machine saw blades up to a weight of 20 kg.
PROCESS ORGANISATION. TOTALLY TAILORED TO YOU.
Tooth face and tooth tops or side – what you machine and in what order is entirely up to you. The VOLLMER automation concept gives you free rein to decide what order the machining steps follow, and the order for processing the loading carriages. One batch or several batches are no problem. The diameter, number of teeth and tooth geometries can be changed as needed. This is particularly economical for small quantity batches.
EXTERNAL PROGRAMMING. NOT A PROBLEM.
All jobs can be programmed and executed on an external input station using the DES 400 data entry station. You do not even need to be in the same room. Alternatively, or if required, you can also program the saw blade stack directly on the loading system, in addition to the external data entry station.
THE SEQUENCE
- Set the saw blades down on the loading carriage
- Select the planned automatic sequence on the control desk
- Enter the saw blade data on the data entry station
- Start the automatic program
- If needed, change the transport carriage with machined saw blades during machining – and grind around the clock

DNC
To manage programs that have already been written centrally, and to be able to use these across several machines, DNC operation is available, which is operated on the customer's own EDP system.
MACHINE AND PRODUCTION DATA ACQUISITION
Additional security for the entire production process is provided by the functions already implemented in the control for acquiring machine and production data. This enables evaluation of machine utilisation and productivity, as well as the storage of tool data.
DIGITAL REMOTE SERVICE
Simple fault diagnostics and user support through remote access to the user interface.
VOLLMER INSTRUCT
This provides targeted help in the event of a fault or when preparing for future service tasks.
OPERATOR NOTIFICATIONS
Store communication relationships and connect to machine parameters. Receive automated notifications on various devices and display values in a standardised format. Use prefabricated processes or easily create your own flows using the Node-RED open-source system.
STANDARD PROTOCOLS
Standardised interfaces and protocols (e.g. OPC UA, MTConnect) mean that data can be effortlessly exchanged between our machines and your applications.
VOLLMER DASHBOARD
The VOLLMER Dashboard for visualising machine data: Access live detailed machine status information. At any time, from any device, from anywhere in the world. You always maintain an overview of the basic data of your machines and the machine utilisation. And you therefore achieve the highest degree of transparency.
IoT-Gateway
With the IoT gateway as a hardware component, the digital world is completely open to you.
DES 400 DATA ENTRY STATION
The DES 400 enables you to prepare jobs at an external workstation while the machine is running, allowing you to make even more productive use of the machine.
SERVICING AND MAINTENANCE.
The CS 860 and CSF 860 are not just incredibly flexible to use, and simple to operate, they are also particularly practical when it comes to servicing, maintenance and repair. We at VOLLMER fully focussed on this aspect during development, to make it hassle-free for you. All maintenance elements are clearly arranged in one place; the control cabinet, pneumatics and fire extinguishing and coolant systems are easily accessible. And if a component simply needs to be replaced, this can be done quickly and easily.
SUPPLY OF WEAR AND SPARE PARTS
The use of tried-and-tested VOLLMER components guarantees consistent quality and quick procurement of wear and spare parts.
OPTIMAL ACCESSIBILITY
The control cabinet, pneumatics and fire extinguishing and coolant systems are easily accessible for maintenance tasks. All maintenance elements are grouped in a single location.
AUTOMATIC CENTRAL LUBRICATION
For low-effort maintenance.
PNEUMATICALLY CONTROLLED AUXILIARY FUNCTIONS
No hydraulic system, no oil change, no oil filter replacement, which reduces the maintenance required. This is not only simple, it is much cleaner.
IDENTICAL CONSTRUCTION
The access and layout are identical on both machines. This simplifies the maintenance routine and reduces the effort required.
THE MOST ADVANCED SERVO TECHNOLOGY
All machines feature the most advanced servo technology with single cable technology – this is safe and powerful, and saves space and energy.
SIMPLE COMPONENT REPLACEMENT
Control components do not require any preconfiguration. This enables spare parts to be procured quickly and, in the event of a fault, allows easy component replacement with quick detection of faults.
V@dison: DIGITAL SOLUTIONS – PRECISION IN TRANSFORMATION
Do you want to optimise your processes with smart technologies, avoid mistakes and reduce downtimes? We offer grinding and sharpening machines that are equipped with an IoT gateway as standard. Contact your VOLLMER representative or find out more now at:
www.vollmer-group.com/en/products/digitalisation
Your Contact
Josef-Loroch-Str. 1
69509 Mörlenbach
Germany
Phone: +49 6209 71590
Fax: +49 6209 715938
info@loroch.de