We detected, that your browser supports another language than the called one. This page is also available in your language! Would you switch to this page in your language?
"In the saw mill, CS and CSF are the ideal sharpening partners" 2023-05-15
to overviewThe carbide-tipped circular saw is indispensable for cutting wood, metal and composite materials. To sharpen them with high precision, the sharpening specialist Vollmer is developing innovative grinding machines: The new generation is called CS 860 and CSF 860. Vollmer Product Manager Thomas Wenger explains the advantages of the machines in an interview at the start of the wood trade fair Ligna 2023.
Question: Hello Mr Wenger, the Ligna woodworking trade fair can finally take place again this year. As Vollmer's product manager, what message are you coming to Hanover with?
Thomas Wenger: In general, we are pleased to be able to meet our customers from the woodworking industry in person again at Ligna. For my team, it is especially exciting to present our new Vollmer CS 860 and CSF 860 grinding machines live. They can be used to automatically sharpen the tooth faces and tooth tops as well as the flanks of teeth on carbide-tipped circular saws. These circular saws are mainly used in the saw mill on chipping and profiling lines. Such lines cut round timber into edged sawn goods in one operation. In order to saw squared timber, boards or battens individually, the circular saws are usually custom-made. The special designs differ when it comes to cutting widths, log thicknesses, diameters or tooth pitches. Our CS and CSF can sharpen various circular saw blades unmanned and around the clock.
Question: How does the new CS 860 and CSF 860 grinding machine duo differ from the previous models?
Thomas Wenger: Predecessor models like the Vollmer CHD and CHF machines were based on a different design. We have completely revised and redesigned the foundation, housing and kinematics of the CS and CSF. The modular foundation rests on the same polymer concrete base for each machine. The machines consist of
a single unit, ranging from loading and set-up to design and programming. CNC technology, operating philosophy and the latest drive technology are also the same for both machines.
Question: You talk about the "latest" drive technology. What exactly makes drive technology new?
Thomas Wenger: We have converted all spindle drives to servo technologies to improve reliability, speed and efficiency. The servo-controlled grinding spindles are not only more reliable and powerful, but also ensure a higher quality of saw blade machining. Different infeed and cutting speeds can be performed on each tooth, which improves the surface quality of the cut edge and brings more flexibility to the grinding process. By switching to servo OCT technology (One Cable Technology), there is now only one cable. This means that there are fewer cables and switches, less power is consumed and it is easier to change a single cable – which, in turn, reduces service costs. It is also the case that no hydraulic systems are used in either machine, only pneumatic systems. This eliminates the use of hydraulic oil, the risk of spillage, the contamination of the coolant or even service calls such as filter changes.
Question: Everyone is talking about digitalisation in mechanical engineering. What does this look like with the CS 860 and CSF 860? Which functions around Industry 4.0 and IoT (Internet of Things) do the grinding machines master?
Thomas Wenger: We have integrated Industry 4.0 via web-based applications, for example to perform services remotely. This allows machine components and software to be updated remotely. Via the remote system, customers are notified by e-mail when a batch of saws is completed or when there is an interruption in production. Customers can access the active dashboard via a mobile phone or tablet to get the latest status report. The integrated IoT gateway, which is responsible for data communication with the outside world, works with a hardened Linux system and therefore ensures network security.
Question: Doesn't digitalisation and automation also mean that the human factor has less influence and that unmanned processing becomes more error-prone?
Thomas Wenger: Rather the opposite is the case, because the machines ensure stable production processes thanks to three measuring devices: Measuring sensor,
measuring cube and acoustic sensor. First, the tooth is scanned and the acoustic sensor detects whether we have the correct feed. The new measuring cube with absolute fixed point provides information about the position of the grinding wheel. In the event of temperature fluctuations in the machine or spindle, this fixed point compensates for all other parameters. The combination of this closed-loop system with polymer concrete foundation is currently unique in the global grinding market and offers precision measurement technology that has a repeatability of 1 µm.
Question: High precision is certainly necessary in the metal sector, but does the wood industry or the sawmill owner need such high precision for their circular saws?
Thomas Wenger: The CS and CSF are particularly in demand in saw mills, where carbide-tipped circular saws are increasingly being used on chipping lines. These saws are usually custom-made with their own tooth geometry, broaching cutters and offset bodies. Our machines feature R2 axles for axial cross adjustment, centre brakes for opening blade clamping and rotating pick-up systems to protect broaching cutters. This means that completely different circular saws can be sharpened in the saw mill with a Vollmer ND handling system, unmanned and overnight. In addition, we at Vollmer are convinced that the trend towards more automation will also continue in the saw mill in order to reduce floor space, cut production costs and improve energy efficiency. And for this, our CS and CSF are the ideal sharpening partners in the saw mill.
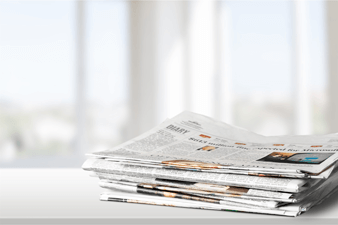

Your Contact
VOLLMER WERKE Maschinenfabrik GmbH88400 Biberach/Riß
Germany