We detected, that your browser supports another language than the called one. This page is also available in your language! Would you switch to this page in your language?
Several thousand customers worldwide already rely on VOLLMER expertise and are successfully using our technologies.
You can read some of these success stories here – clearly structured according to the various product ranges.
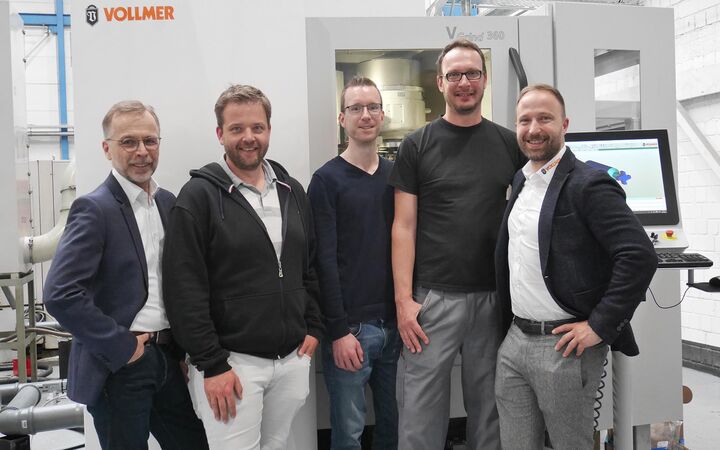
InduGrind and VOLLMER – a partnership for increased sharpness
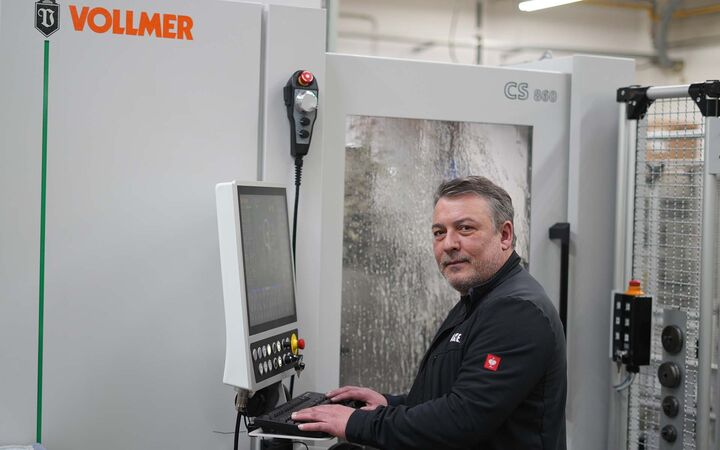
A pair of machines from Swabia for the perfect circular saw blade
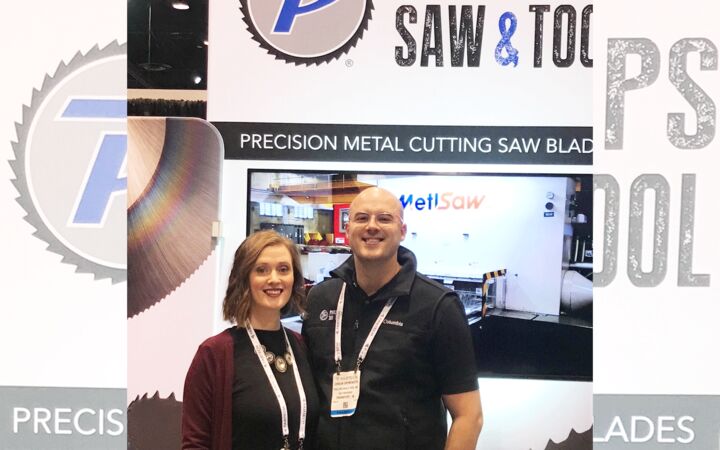
Frankfort residents rely on VOLLMER and Loroch
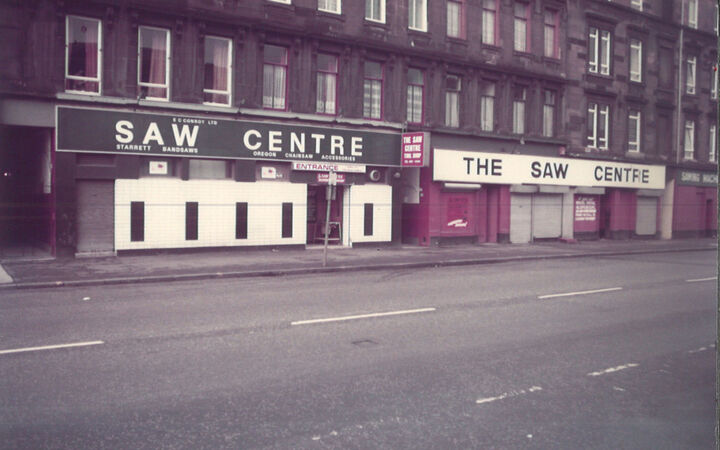
Saw Centre Cuts Path to Productivity with VOLLMER
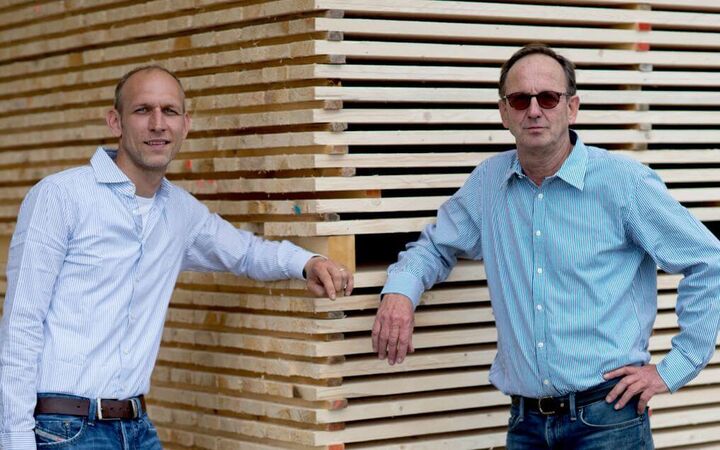
Swabian technology for wood processing
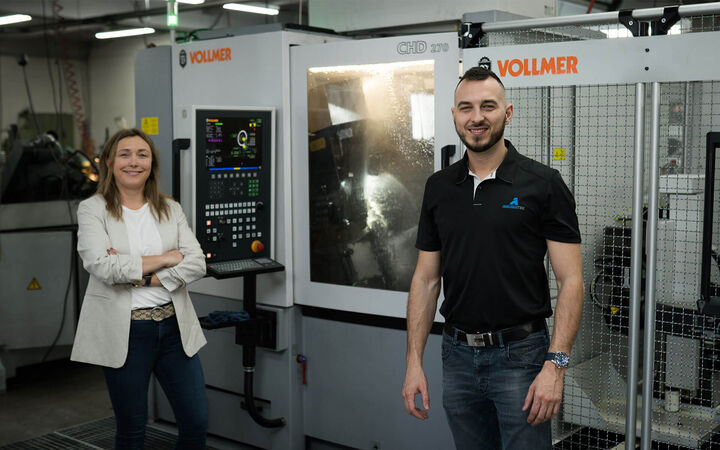
Looking across the waters at Canada, Aiguisatek is overcoming the coronavirus crisis with some help from VOLLMER
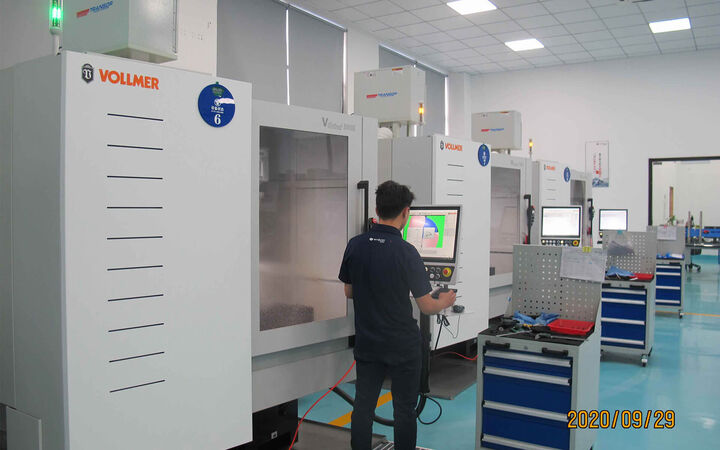
Tool manufacturer from China is placing its trust in VOLLMER
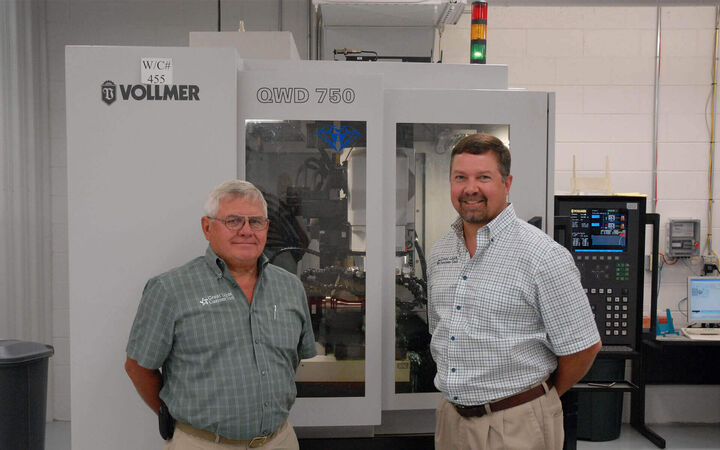
Toolmaker at the Great Lakes puts its trust in VOLLMER
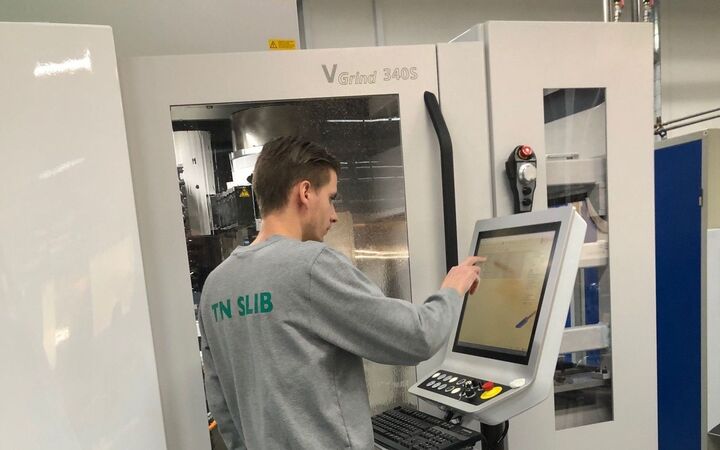
Dänischer Werkzeughersteller vertraut auf VOLLMER
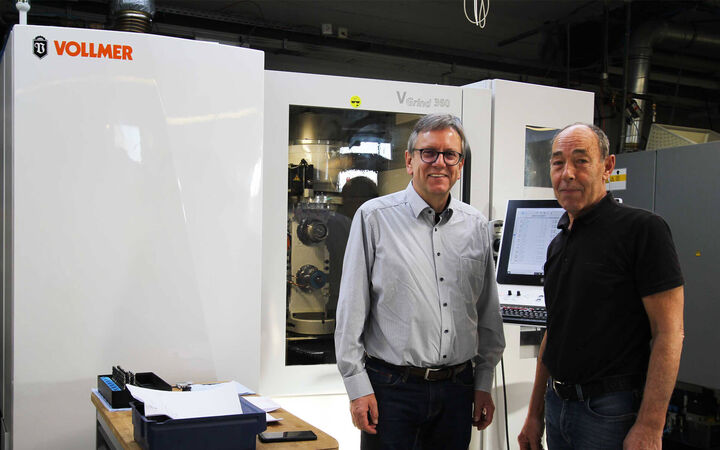
Schrode is relying on Swabian sharpening technology from VOLLMER
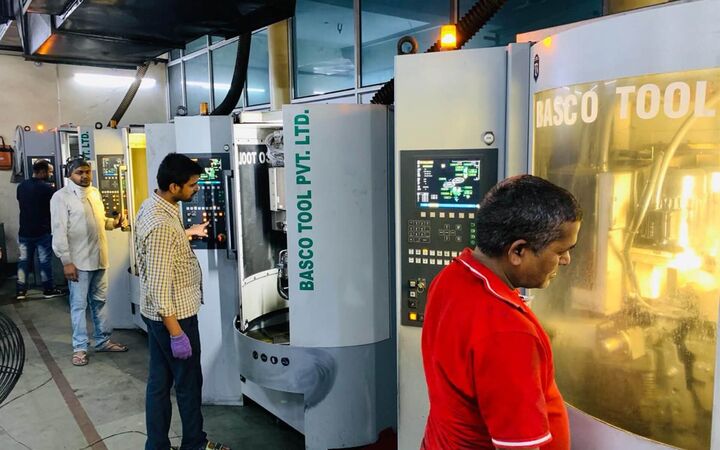
Circular saw blades carve out a path for India's economic boom
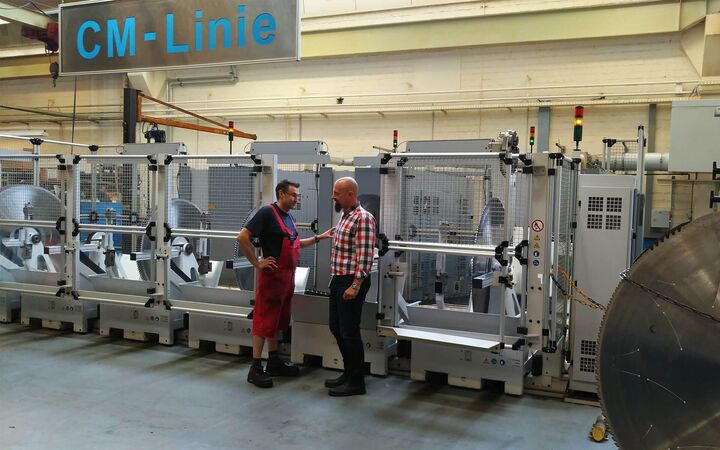
Saw blade manufacturer Lennartz uses VOLLMER sharpening technology
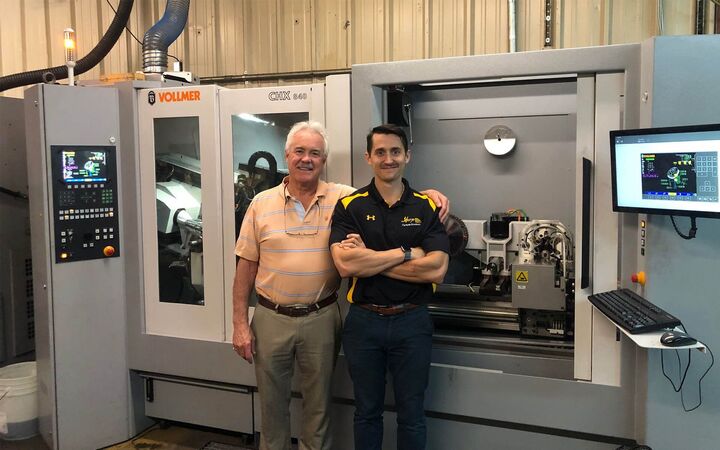
Saw manufacturer Sharp Tool sharpens its focus with VOLLMER
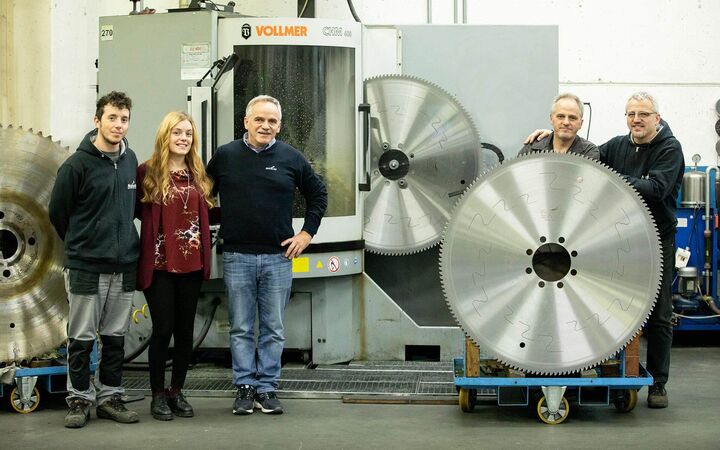
Italian saw blade manufacturer puts its trust in VOLLMER
Swabian machining expertise
Sharpening machines communicate thanks to IoT gateway
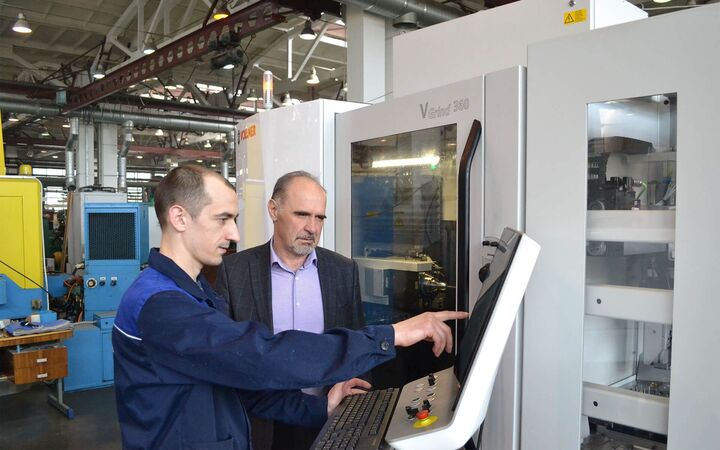
Siberian toolmaker relies on Swabian sharpening technology
Japanese toolmaker relies on VOLLMER sharpening technology
Sharpening saw blades at the Yellow Sea
When Swabians sharpen special tools
Dutch company sharpens circular saws with Swabian technology
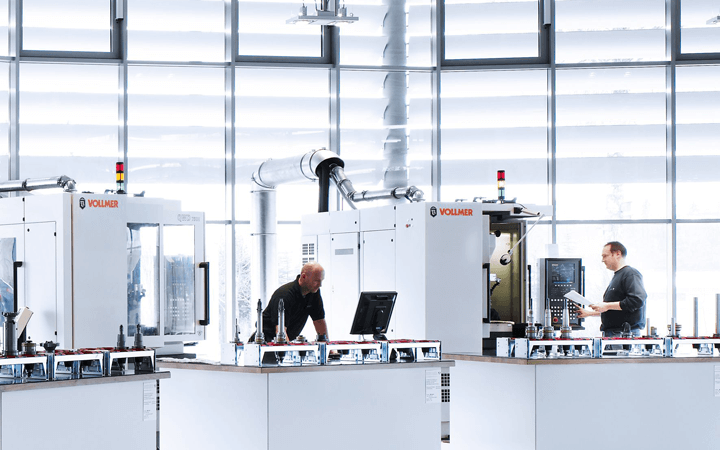