We detected, that your browser supports another language than the called one. This page is also available in your language! Would you switch to this page in your language?

WALL CONCEPT
Very rigid, compact construction with optimal accessibility and overview for the operator.
MULTI-LAYER MACHINING
Two vertical grinding spindles with the grinding wheel set at the C axis pivot point. Reduced machining times thanks to shorter linear-axis travel distances.
MODERN OPERATING CONCEPT
Height-adjustable, with touchscreen, 19" diagonal screen size and optimum view into the machining chambers.
NUMROTOplus®
The reliable, intuitively operated software with 3D tool and machine simulation, combined with collision monitoring.
GRINDING WHEEL CHANGER
Provides even more flexibility in your manufacturing processes – with eight HSK-50 grinding wheel sets. Both grinding spindles can be loaded with complete flexibility.
AUTOMATION
The VOLLMER HP 170 pallet magazine, the HPR 250 free-arm robot or the HC 4 and HC 4 plus chain magazines automatically ensure increased capacity and flexibility.
TORQUE
Higher torque at the bottom spindle for powerful fluting operations and an increased material removal rate.
LINEAR INDUCTION MOTORS
Linear induction motors on the X, Y and Z axes allow for high precision and energy without wear.
FOR INCREASED PRECISION AND PERFORMANCE
The VGrind 360S – the new standard for the complete machining of solid carbide tools of up to 200 mm. Ideal for applications in the areas of automotive manufacturing, toolmaking, medical technology, precision engineering, aeronautical engineering and many more.
What sets this grinding machine apart is that it has more precision and power thanks to its innovative linear induction motor on the X, Y and Z axes. This allows you to use the vertical multi-layer machining to bring all of the machine's assets to the fore – with magnets, without making contact and without wear. This results not only in excellent performance, but also less maintenance required.
What you get: Optimal surface quality thanks to a five-axis grinding machine which impresses with every detail – from the operating concept to the intuitive software and clever automation solutions.
THE APPLICATION
The VGrind 360S has been designed for productive machining of carbide drills and milling cutters with diameters of up to 32 mm. Depending on the machine kinematics and the tipping of the grinding wheel packages, tools with diameters of up to 200 mm are also possible.
The high flexibility provided by the possibility to change both grinding wheel packages, the reduced changing times thanks to the positively guided system and the practical automation options, combined with the high torque at
the bottom spindle for fluting operations, provide the best prerequisites for efficient and high-quality manufacturing.

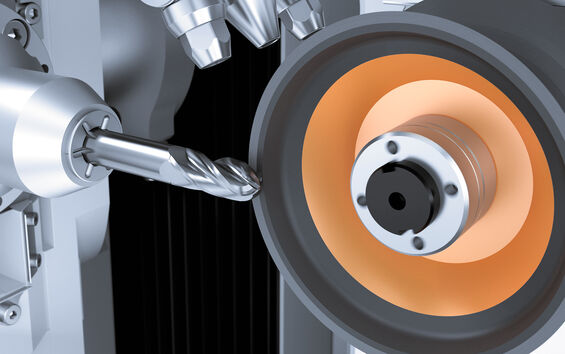
THE MACHINE CONCEPT
Precision and efficiency squared: This principle is also followed by the VGrind360S – thanks to two vertically arranged grinding spindles. In addition, its effective cooling concept has now been optimised and extended. The result: Maximum perfection at the lowest tolerances with the best possible cooling.
- Five-axis CNC grinding machine with innovative kinematics
- Two grinding spindles situated one above the other with the grinding wheel set positioned at the C axis pivot point – to ensure extremely precise grinding results
- The vertical spindle arrangement solves the well-known problems related to fixed and floating bearings
- Higher torque at the bottom spindle for fluting operations
- Wear-free linear induction motors on the X, Y and Z axes not only guarantee lasting consistency of quality and lower maintenance costs, but are also the key to improved surface quality
- Innovative wall concept with the highest possible rigidity and outstanding damping thanks to polymer concrete
- The innovative heat exchanger effectively cools the motors and spindles. This increases the thermal stability and optimises precision and performance in the long term
- Both spindles can be fitted with multiple different grinding wheel configurations. The automation option ensures seamless conversion
Further options
- Flexible automation options for carbide tools
- Grinding spindle available with direct or belt drive
- Wheel compensation probe: Grinding wheel alignment and wear control within the machine
- Automated changing of intermediate sleeves with bayonet
- Simultaneous grinding wheel package and tool change in combination with the HP 170 pallet magazine or the HC 4 and HC 4 plus chain magazines reduces non-productive times during loading
THE OPERATING CONCEPT
In order to be able to exploit the full potential of your VGrind 360S, simple and intuitive operation is vital. This begins with the control panel, which is positioned on the VGrind 360S so that not only the LCD display, but also the working area can always be observed in the best possible manner. Operation via the keyboard or touchscreen allows for precise machining of the tool. The multifunction handwheel ensures even more flexibility: It can be freely positioned on the enclosure and is designed for setting a required axis – without using the control panel. In short: With the VGrind 360S, it becomes a pure delight to achieve the best results.
ERGONOMIC OPERATION
- Flexibly height-adjustable swivelling control panel
- variable multifunction handwheel
- optimal view into the machine
- easy access to grinding spindle
SOFTWARE NUMROTOPLUS®
VOLLMER consciously opted for a well known software system that is already established on the market. The logically structured interface guarantees intuitive handling. With established programming systems, a huge variety of tools can be manufactured and resharpened. You can change any detail of your tools and adapt them to your individual requirements.
Fully informed: Thanks to a perfect 3D simulation of the tool and machine. And with collision monitoring, you can always stay on the safe side.
AUTOMATION
Work process automation is one of the key factors of modern tool production. With the VGrind 360S, you can choose from a range of excellent equipment options. This allows you to implement large batches of your tools and to make
your manufacturing processes quicker, safer and more precise.
The various automation options that we offer enable you to optimally adjust the VGrind 360S to your requirements.
Always supply the right grinding wheel – with no manual intervention required: The optimum automation system for eight grinding wheel sets. As an option, coolant nozzles can be automatically exchanged with the wheel sets on both spindles. This is a vital contribution to productivity within your manufacturing process. The oriented spindle holder automatically positions the new grinding wheel packages in the same location on the grinding spindle. This reduces planing and run-out errors and therefore increases the tool's precision.


Your Contact
Orchard Park Ind. Estate
Town Street, Sandiacre
Nottingham NG10 5BP
United Kingdom
Phone: +44 115 9491040
Fax: +44 115 9490042
info-uk@vollmer-group.com