We detected, that your browser supports another language than the called one. This page is also available in your language! Would you switch to this page in your language?
Swabian technology for wood processing 2021-09-28
to overviewThe Holzwerk Baur saw mill, based in Wain, Upper Swabia, processes around 180,000 solid cubic metres of wood each year, and exports its products across the world. Sustainability is a key priority for the saw mill. The wood is sourced in the region, and every last shaving is put to use. To ensure the wood is cut efficiently, Holzwerk Baur runs around 250 saws every day, kept sharp using machines supplied by Biberach-based sharpening specialist VOLLMER. Amongst the many machines in the filing room is a VOLLMER CHD 270 grinding machine for carbide-tipped circular saw blades, set up with an automated system to run around the clock.
Holzwerk Baur, based in Wain, is a firm with a long history. In 1900, Bartholomäus Baur founded his carpentry workshop. He expanded this into a saw mill two years later, now run by the fifth generation of his family, his great-grandson Hermann Baur and great-great-grandson Frederik Baur. A medium-sized enterprise with around 90 employees, the saw mill cuts around 180,000 solid cubic metres of wood and has the capacity to store 10,000 solid cubic metres of logs. The production area extends over 100,000 square metres – the equivalent to about 15 football pitches.
Sustainable forestry and timber industry in Wain
"It is not just our family which has a long tradition of processing and finishing wood. The whole area around Wain is part of this tradition," explains Frederik Baur, CEO of Holzwerk Baur. "The 'Lords of Wain' have been cutting down wood in the local forests for more than 500 years. We have set ourselves the goal of ensuring a long-term future for wood processing, which is why we source our wood exclusively from sustainable forestry."
Holzwerk Baur only purchases its logs from responsibly managed forests, based within a radius of 100 kilometres around Wain. Suppliers are state, municipal and private forest owners. Customers, however, are based all over the world, with demand for wood being especially high in China and Russia at the moment.
Swabian partnership in the saw mill
The wood industry is such a part of the tradition of this community of 1600 people that it even features in Wain's coat of arms. The chevron of wood harks back to the coat of arms of the "Lords of Wain", who once resided in the town's castle and palace. Whilst the castle is long gone, the tradition continues to this day, with the palace being the home of the baron of Herman auf Wain's financial administration and forestry management office. The village itself is in the district of Biberach, which is also where many of the machines that have been used in Holzwerk Baur for decades hail from.
"The filing room at our saw mill contains VOLLMER sharpening machines from Biberach – some of which have been working here longer than I have!" says Hermann Baur, joint CEO of Holzwerk Baur. "The most recent success is a CHD 270 grinding machine for carbide-tipped circular saw blades, with an automated system which allows it to run around the clock, largely without manual intervention."
Carbide-tipped circular saws for cutting wood
Holzwerk Baur has 250 saws in operation every day, each of which needs to be resharpened after one and a half shifts. The VOLLMER CHD 270 is a grinding machine with eight CNC-controlled axes and measuring equipment able to machine carbide-tipped circular saw blades in a single set-up. It is able to sharpen even complex tooth geometries, including chip breaker grooves, chamfers on the precutting and finishing teeth, Braunschweig tooth or chip guide notch. Every circular saw blade is loaded into its precise grinding position automatically, regardless of its diameter. A measuring sensor then determines the tooth geometry, in other words the hook angle, radial and tangential clearance angles, cutting width, blade thickness and side projection. The grinding machine is automated using the VOLLMER ND 320 handling system, which uses two loading carriages, each of which can be loaded with up to 50 circular saw blades.
Production cycle optimised for every trunk
For Holzwerk Baur, the VOLLMER sharpening machines are the key to sustainable wood processing, which begins with stripping the bark from the logs when they arrive at the saw mill. The company has created a production cycle which ensures optimum use is made of every trunk, with practically every piece utilised. Able to process 80 metres per minute, the profiling line cuts the logs into clean squares, which are then processed by up to ten saw blades into boards, frames and floorboards. This sustainability extends to recycling. Every last scrap of wood is used, with wood chips going to the paper mill, sawdust to chipboard manufacturers, wood shavings to the filler industry, and bark to gardening and landscaping firms or to their own heating system. A combined heating and power plant is currently being built at the Holzwerk Baur site, designed as a highly efficient way to meet all of the saw mill's heating and power needs.
"Holzwerk Baur is an impressive example of how a modern German saw mill can operate successfully on an international level, and of the role VOLLMER sharpening technologies can play in this success," says Jürgen Hauger, CEO of the VOLLMER group. "Our sharpening machines are used throughout the wood industry for machining circular saws, band saws and cutting tools, and are equally at home in saw mills and in the furniture construction or the steadily growing house construction sectors."
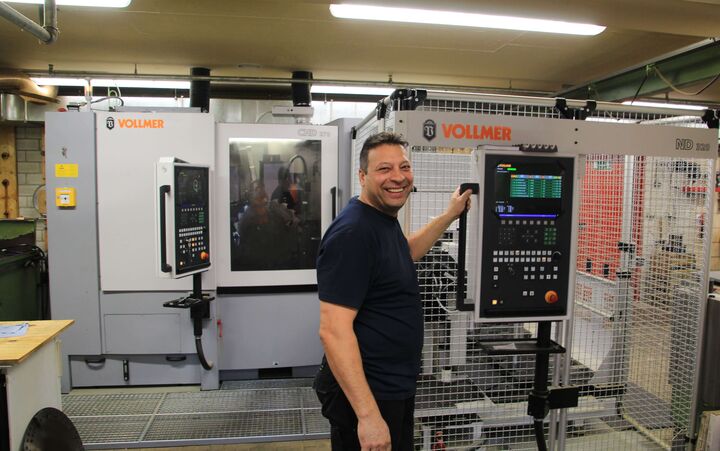
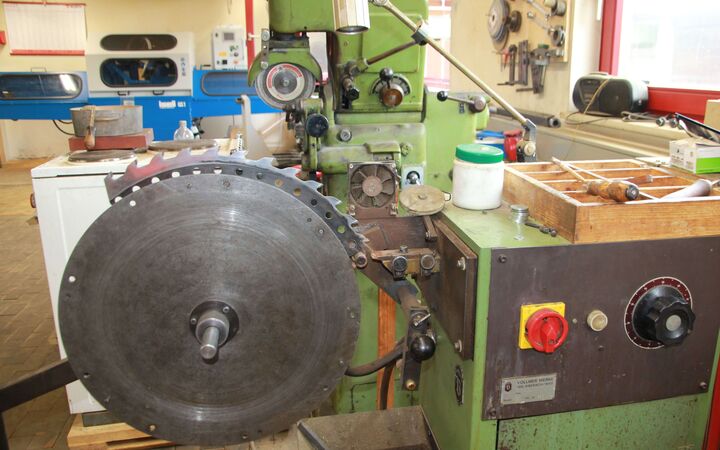
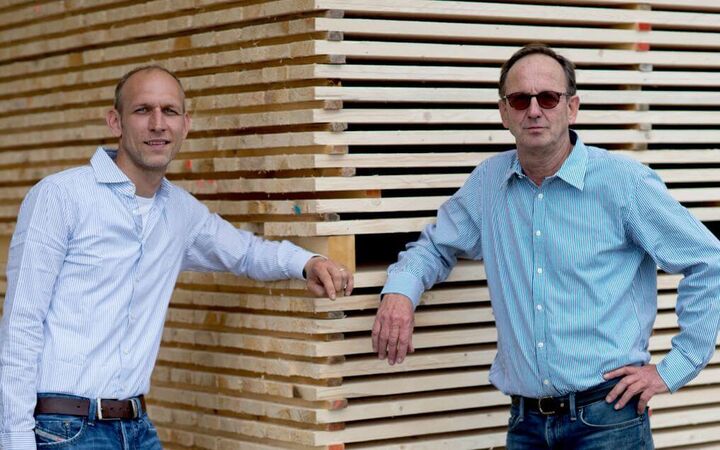
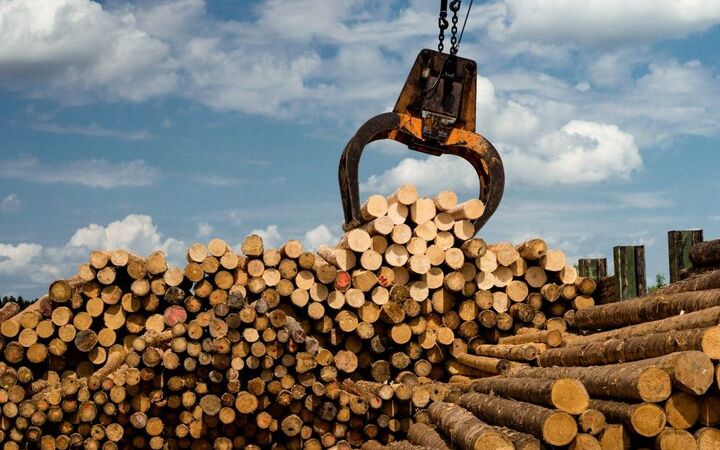

Your Contact
VOLLMER UK LTD.Town Street, Sandiacre
Nottingham NG10 5BP