We detected, that your browser supports another language than the called one. This page is also available in your language! Would you switch to this page in your language?
A pair of machines from Swabia for the perfect circular saw blade 2023-02-16
to overviewThe Swabian towns of Balingen and Biberach are separated by less than 100 kilometres. One is home to tool manufacturer AKE Knebel, the other to sharpening specialist VOLLMER. Both companies have dedicated themselves to the sharpness of circular saw blades and tools. While VOLLMER manufactures sharpening machines for this purpose, AKE produces around 250,000 carbide-tipped circular saw blades per year. In addition to the traditional areas of application, a significant number of them are used in sawmills for cutting raw wood on chipping lines.
AKE is represented at 40 locations worldwide
When it comes to circular saw blades, AKE has more than 60 years of experience. Since being founded by Albert Knebel in 1960, the tool manufacturer has grown into a global player in the production of circular saw blades and rotary tools. Internationally, AKE has more than 40 sites and employs around 320 people in Germany and more than 500 worldwide. In Germany, the company is represented not only in Balingen, but also in Rietberg in North Rhine-Westphalia and Prien in Bavaria.
Each year, around 200,000 carbide-tipped circular saw blades leave the factory in Engstlatt near Balingen – around half of them are custom-made. The metal and plastics sectors, as well as the furniture and wood industries, rely on the precision of these circular saw blades and other tools manufactured by AKE. At Ligna 2023, AKE presented its new generation of saw blades from the Boardline range. It is suitable for industrial board cutting of coated and uncoated wood materials as well as multiplex and HPL boards (high-pressure laminate).
"We rely on the grinding machines from VOLLMER for the sharpening process precisely because around 50 percent of our products are custom-made. With them, we can grind any saw tooth geometry, no matter how complex, fully automatically and with the highest precision," says Emilio Tortora, Production Manager at AKE Knebel.
In the sawmill, chipping and profiling lines process round timber into trimmed sawn goods such as squared timber, planks, boards or battens in a single operation. Here, feed rates of up to 200 metres per minute are achieved, which are only possible using high-quality circular saw blades. These specific cutting tasks require appropriately designed circular saw blades, which is why at AKE an order usually starts with an in-person customer meeting to find out about the specific cutting process.
"Talking to our sawmill customers is all about listening and understanding so that we can make the perfect circular saw blade for the required wood cutting process," adds Emilio Tortora. "We manufacture the entire carbide-tipped circular saw blades ourselves in our Engstlatt factory, from the lasered basic body to the sharpened saw teeth."
Around 40 VOLLMER sharpening machines for the circular saw blades
Individual means that the circular saw blades differ in their cutting widths and blade thicknesses, that they have different diameters and tooth pitches, and that their saw teeth end up with customised geometries. In the beginning, AKE even developed its own grinding machines for the sharpening process under the Akemat brand. More than 20 years ago, AKE handed over the division to VOLLMER, the machine manufacturer whose sharpening machines dominate the production hall today.
AKE currently owns around 40 VOLLMER grinding machines – only in the last few months has the tool manufacturer commissioned nine new VOLLMER machines from the CS 860 and CSF 860 series. They can be used for machining the tooth faces and tooth tops, as well as the flanks of carbide-tipped saw teeth. Both machines can be controlled and programmed intuitively via the touch screen or keyboard thanks to the tried-and-tested VOLLMER operation. The advantage for AKE is that the machines automatically detect the geometry of a saw tooth and sharpen it to size using oscillating machining. For automation, AKE decided on a VOLLMER handling system from the ND series. The robot system can combine up to three grinding machines and, depending on the equipment, can be loaded with up to 650 circular saw blades.
PCD-tipped circular saw blades for a long service life
For its PCD-tipped (polycrystalline diamond) circular saw blades, AKE uses the VOLLMER QR 270 and QF 270 erosion machines. Diamond circular saw blades impress with their long service life and wear resistance. Their full potential is unlocked when cutting cement fibre boards or recycled wood. Since recycled wood, for example, is obtained from wood chips and wood shavings from waste wood, chipboard may still contain mineral residues of construction materials such as gypsum or cement. These can also be cut safely and precisely using PCD circular saw blades.
"What we appreciate about VOLLMER is not only the high-precision grinding machines but above all the cooperation based on partnership and the prompt on-site service. One call is all it takes and a service technician will be with us in no time," says Alexander Knebel, son of the company founder and current CEO of AKE Knebel. "This is exactly the same service principle that we follow with our customers so that we can always supply the perfect tool for wood or metal cutting."
Producing PCD rotary tools with VOLLMER machines
While AKE produces circular saw blades in Balingen, the company manufactures rotary tools such as chippers, bore cutters and end mills in Rietberg. Rietberg is also home to a good dozen VOLLMER machines that give the PCD-tipped tools their sharpness. Among others, there are disc erosion machines from the QXD series as well as wire erosion machines from the QWD series. PCD cutting edges are machined without contact using wire erosion. AKE's rotary tools are used for machining plastics, metal, composite materials and wood. They are used in traditional areas of application such as joining, grooving and rebating on industrial machines down to traditional craft machinery, but also on profiling lines, for example, to automate the milling of tongue and groove for floor coverings such as parquet and laminate.
"In the sawmill, the carbide-tipped circular saw blade has been unsurpassed for wood cutting for decades and will become even more important due to state-of-the-art chipping lines," says Jürgen Hauger, CEO of the VOLLMER Group. "The cooperation with AKE shows the role our CS 860 and CSF 860 grinding machines play in the production and resharpening of circular saw blades in the filing room of a sawmill."
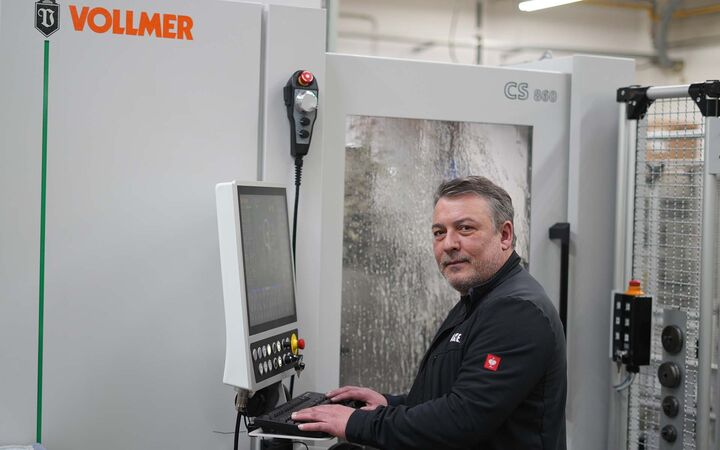
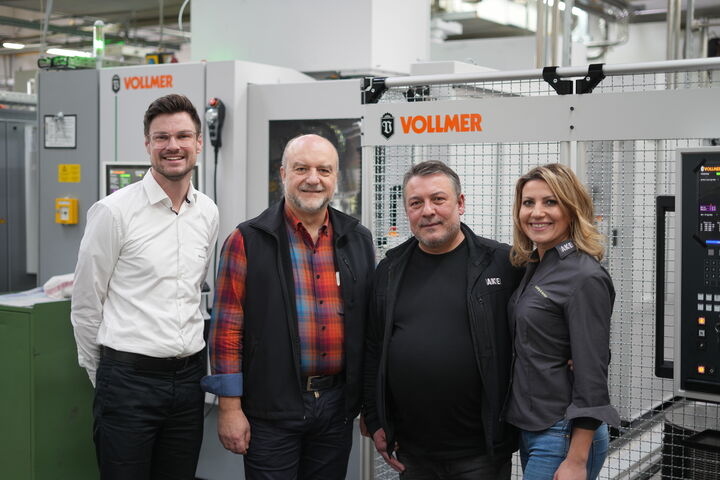

Your Contact
VOLLMER UK LTD.Town Street, Sandiacre
Nottingham NG10 5BP